Gambar Design lemari buku ini penulis gambar melalui media soft
ware Auto CAD 2007,3 DSMAX versi 2011
Friday, December 27, 2013
Tuesday, December 24, 2013
Monday, December 23, 2013
screw jack by dian pramesti
Is the jack screw jack screw system to raise or lower the donkrak . At this screw jack , to raise or lower the screw jack rotating Screw enough . By turning a threaded pinion gear will rotate gears umbrella , round umbrella gears will rotate grooved tube , then rotate the threaded rod which in turn rotate the screw jack to move up or down in accordance with the minimum and maximun limit of the specification screw jack itself.
Working drawings screw jack
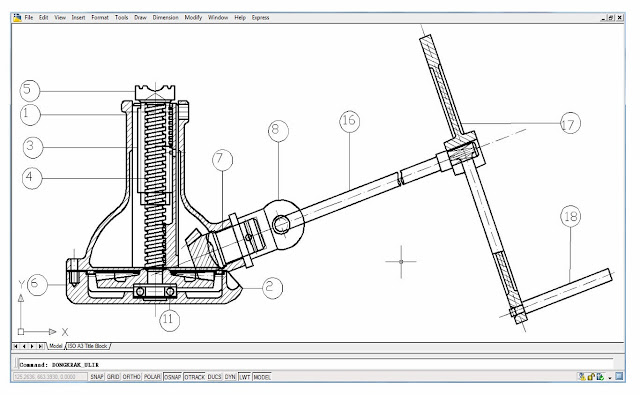
Figure threaded assemblies screw jack
Number section - the main part of the screw jack
1 . framework
2 . anvil
3 . grooved tubes
4 . threaded rod
5 . threaded tube
6 . Umbrella gear
7 . pinion gear
8 . connection
11 . bracelet steel ball bearings and axial
16 . pivot player
17 . holder
18 . arm holder
To move up and down As well there should be a round jack , such as tightening or loosening a bolt, then the holder and the handle holder is required to rotate the screw jack .
Generally the tip forming question mark " ? " , For screw hook into the player , while the other end is more like a letter " Z " or " L " , to facilitate turning the jack .
Sunday, December 22, 2013
Streamlined 3D data delivery cuts costs, saves time
With plants and distribution centres in Auckland
and Sydney and the capacity to produce over
700,000 pieces of furniture per year, Criterion
Group Ltd is the largest manufacturer of ready-toassemble
furniture in Australasia. An innovative
design team, state-of-the-art technology and over
40 years’ experience in the furniture industry
enable the company to produce cutting-edge
designs that are excellent value, functional, easy to
assemble and look great. With design playing such
a crucial role in the company’s business, fi nding
ways to streamline the sharing and processing
of 3D designs across varied operations is critical.
Autodesk worked with Criterion to implement
a new Autodesk Inventor Series platform that
allowed the furniture expert to do just this,
producing savings in time and cost.
Constant upgrades keep Criterion at the cutting
edge
Criterion’s aim is to design and produce furniture
that makes homes and offi ces more attractive and
functional. The company’s success is based on a
design philosophy that adapts the latest trends in
furniture style and functionality to meet specifi c
customer needs. With its strong emphasis on
design, it is key for the company to continually
invest in the latest technologies and most
sophisticated equipment.
Integration of 3D design data was a no-go
A recent improvement that the company wanted
to make was to integrate its 3D design data with
the various types of machinery and CAM packages
it uses. However, many woodworking machines
and their related CAM solutions do not allow the
direct import of 3D data. Criterion was therefore
forced to manually create a special data fi le for
each machine or system, a process that takes
around 30 minutes.
In addition, Criterion had recently purchased an
advanced, high-productivity drilling line, which
required that design data be imported in a very
unique way. Furthermore, production machinery
was becoming increasingly computer-controlled.
Criterion recognised that if the import of 3D data
to machinery and systems could be streamlined, it
would save both time and costs.
New Inventor platform supports 3D data batch
processing
Criterion’s relationship with Autodesk dates back
to the early 1980s — the company was one of the
very fi rst users of AutoCAD in New Zealand. Not
surprisingly then, Criterion approached its longtime
partner Autodesk with its problem, and after
discussion with the reseller — CADPro Systems Ltd
— a brief was developed.
Criterion wanted to leverage the highly intelligent
3D design data from Autodesk Inventor Series and
feed that information directly into the controller
for the new drilling line. Autodesk’s Professional
Services (APS) Team worked together with
Criterion’s engineers to scope out the desired
solution. APS delivered customised code to extend
the capabilities of Inventor and allow a simple
interface to export the data directly into the new
drilling line in the correct fashion.
This new integrated engineering process means
that a task that once took 30 minutes to complete
now takes less than fi ve minutes.
Friday, December 20, 2013
Thursday, December 19, 2013
Monday, December 16, 2013
DDUNIT SETTING IN AUTO CAD BY BUDI MARYANTO
Drawing a building in accordance with what we expect is not an easy thing. From planning, to interior and exterior models we may need a lot of time and consideration to complete. But one thing that is not less important in making drawings of the building must not be separated from the unit unit. Because this unit unit would you use to adjust the size of the system in the image of a building that have previously been planned.
We can control the type of notation units we need.
AutoCAD on the state of wear standard decimal notation in
determine the coordinates, distances, and angles. However, the choice
Other notations are also available.
steps for setting unit unit is:
1. Open autocad then> new file (Ctrl N)
2. Type DDUNITS units or on the command line to run the command, then press enter so that units Drawing dialog box appears.
3. Make sure the Length group, we choose to type Decimal and precision we pilih0.00.
4. At Angel group, we choose to type the decimal precision Degrees and 0.
5. For Clockwise left blank.
6. For Insertion scale we choose units milimeters.
Well after all the settings are finished and then we select ok to close the dialog box. Thus we have succeeded in setting up units Units that will be used for system sizes in our drawing.
Description:
1. Length - Type, allowing us to determine or select the unit system that we use.
2. Precision, the level of precision of our chosen unit can be determined by pressing the arrow in the lower precision.
3. Angle - Type, to determine the precise level of the system and have the same way with Length - Type.
4. Direction, to determine the direction of the corner. In AutoCAD used "counter clockwise" or berlawananarah clockwork.
5. Can we assume the value of the unit by kebutukan kita.Contoh: 1 units can be considered as 1 meter or 1 cm or 1 inch, and so on. This relates to the international standards used reference pencetakan.Dalam 1 unit = 1 mm. We can control the type of notation units we need. AutoCAD on the state of wear standard decimal notation dalammenentukan coordinates, distance, and
angle. However, another notation options available as well.
Friday, December 13, 2013
tips Relaksasi Selama Masa Kehamilan
Tips dari Zwitsal:
·
Nikmati waktu sendiri! Olahraga selama masa kehamilan bagus untuk Bunda
dan untuk bayi dalam kandungan: si Kecil memperoleh makanan yang cukup
dari peredaran darah Bunda yang lancar dan baik. Jadi usahakan sebanyak mungkin
berjalan-jalan di udara terbuka. Berenang adalah olahraga yang baik. Hindari
olahraga yang rentan guncangan, seperti lari/jogging atau berkuda.
·
Perhatikan postur tubuh. Berjalan atau berdiri dengan punggung
membungkuk akan menimbulkan sakit punggung. Jangan memakai sepatu berhak
tinggi, jangan meregang lutut terlalu sering dan jangan melakukan gerakan
tiba-tiba selama masa kehamilan.
·
Ikuti kegiatan senam hamil, yoga dan renang. Ini sehat dan membuat nyaman.
Bunda bisa belajar santai dan semua persiapan melahirkan dengan tenang.
·
Bersantai dan tidur sejenak jika menginginkannya. Postur tidur yang baik
adalah tidur dengan posisi menyamping/miring, dengan lutut sisi atas menekuk.
Letakkan bantal untuk menyangga perut dan lutut yang ditekuk.
·
Manjakan diri, makan di luar rumah atau pergi ke salon/spa. Jika pergi
liburan: pergi menggunakan pesawat terbang dapat dilakukan hingga kandungan
berusia 7 bulan. Beri diri sendiri sedikit kemewahan dan nikmati masa
kehamilan!
Wednesday, December 11, 2013
Wednesday, December 4, 2013
HAND DRILL by Budi Maryanto
Hand drill is one of the machining tooling equipment that serves to make a hole in the workpiece. Hand drill used for working objects of material soft material, not the material used for hard materials.
Drill hand image
SPECIFICATION DRAWING HAND DRILL
In figure authors draw a hand drill in AUTO CAD 2007, then rendered in 3dsmax 2011 version, with the aim of getting the finest detail.
In figure authors use a hand drill two pinion gear, ring gear and one with a handle connected to the hand.
One piece pinion gear serves to clamp the drill bit holder, which is only to balance the round. Both pinion gear connected to the ring gear on the handle to rotate the holder rigged clamp the drill bit.
Monday, December 2, 2013
COMPUTER SYSTEM FOR CAD by Dian pramesti
Eletronis computer usage at this point has been reached at any stage of the application of the field of engineering . The application fields of engineering is a field that is fixed and changed along with the development of the computer itself .
The incorporation of computers into the design process to the manufacture of prototype example has changed the old way , ie by means of the manual . Method for making a good picture it working drawings and 3-dimensional image with a computer -assisted or in other words the system CAD ( Computer Aided Design ) has provided a very significant role in the world of engineering .
The image of science with computer aids is a very broad field , these fields include the manufacture and use of the pictures are computer generated and may include photography , trade , cartography , animation , publishing , as well as the making drawings and plans
Computer image consisting of a monitor , keyboard , central processing, unit ( CPU )
COMPUTER SYSTEM
A complete computer system comprising:
1 . hard Ware
2 . Soft Ware
3 . Brain Ware
The various parts that make up the physical equipment of computer system known as the Hardware
Program and work orders that allow a computer system to operate in classified as Software . Program categorized as computer - program application programs (application progams ) and operating system (operating system ) . Operating systems such as DOS , Windows , Linux and UNIX is a collection of commands that control the operation of computer systems and auxiliary equipment , as well as the implementation of programs - programs that are specialized .
Program applications is a link between the use of programs - programs that are specialized and their associated tasks , such as creating a plan drawing , desktop publishing and other common systems programs .
The CAD system users have received training on how to use a CAD system to produce images also called Brain Ware
COMPUTER USE FOR AUTO CAD 2007
The selection of the hardware to support the CAD system in its task of drawing is very necessary . This is done , to get maximum results , because a lot of users who use AUTO AUTO CAD CAD to draw 3 -dimensional objects , but to show the real picture detail approaches using 3 DSMAX application program to render up to thousands of frames .
The author has tried , with the draw bolt nut size M 12 X 1.5 in the 3 -dimensional shape in AUTO CAD 2007, because the rendering limit in AUTO CAD 2006 only up to 100 frames , the author tries to picture the size of the bolt nut M 12 x 1.5 in the 3 -dimensional shape is rendered in 3 DSMAX version 7 , with a total of 2500 frames frames , with a low level of computer time allocation is needed in the process of rendering 5 hours . Too long to get a satisfaction
The author recommends to use a mid-level computer programs to AUTO CAD 2007 with the way rendering is done on the program 3 DSMAX version 7 , with processors from INTEL and AMD .
Table Specifications intermediate level computer to AUTO CAD 2007 with rendering using 3 DSMAX version 7 with processors from INTEL and AMD
Friday, November 29, 2013
PROCESS DESIGN by Dian Pramesti
The design is the ability to combine ideas , scientific principles , resources and existing products developed for the settlement of the problems associated with the level of customer satisfaction of the product
The ability to solve this problem is the result of an organized approach and is a regular on the settlement of an issue , this is called the design process
Figure chart design process
The design process always leads to the manufacture , assembly , marketing . many services and activities required for a product that we know . Although many of the industries identified in their own ways , but the most straightforward procedure for the design of new products or improvement of the old design , through the following five stages
1 . Identify the problem
2 . Concepts and ideas
3 . Compromise on the settlement issue
4 . Model or prototype
5 . Image production and working drawings
Supposed to be a walk through the five stages of design mentioned above , if one part can not give good results and useful , it is necessary to find the root of the problem by going back to the original stage and repeat the procedure at each stage .
1 . PROBLEM IDENTIFICATION
Design activity begins with the identification of the problem to the needs of consumers for a product that will be created or improved on certain products . In this case the designer must identify the needs of consumers for a product which is a result of the pendisain.Tentukan if the results of the design will be used by whom ? And how to use it .
2 . CONCEPT AND IDEAS
In this stage , all the ideas that make sense and do not make sense together in one section , for further analysis so as to form a concept of design thinking from an expert on how the design is made ? How much it cost ? How much profit will be in the can ?
3 . PROBLEM TO COMPROMISE SETTLEMENT
In this stage , all the ideas and results that have been collected and has been a concept in mind , the design expert seoarang must have compromise from within ourselves to settle the existing problems .
4 . MODEL OR PROTOTYPE
One form of compromise to the problem is to make a model or prototype.baik through the media or through CAD modeling real form , for example from resin ( fiberglass ) . At this stage prototype that has been made , re- studied the shape , the fabric , the strength of the material , if the design is made to move , it is necessary to carefully re , how the movement , driving source , all these things lead to one goal is to convince yourself that design has been made in accordance with the plan .
5 . FIGURE DRAWING AND PRODUCTION WORK
Once a model or prototype is made the next step is to create production drawings and working drawings . Image production is made as material for a presentation on the design , using a wide variety of applications created on CAD systems , working drawings made to obtain further action on the part that is in the process of the production process , so that the design can actually be realized in the form of a product
Monday, November 25, 2013
Development of prototypes
Prototypes
were developed, based on AutoCAD and the Swedish AEC application Point. In the
resulting applications the structuring of information in layers has been
combined with a model-oriented approach to 2D CAD. Documents are produced using
file references with a model space/ paper space system. All information is
stored on file servers in a company wide network. Files are named and placed
according to a company standard file system.
A simple
user interface, based on prototypes developed earlier by Seamus Gilroy, member
of the ISO working group, was designed for the creation and visibility control
of layers (Figure 6). From lists of allowed codes for each separate field, the
layer name or group of layers is composed. If this specification results in a
layer that is not present in the CAD file, a new layer will automatically be
created.
Figure 6.
FFNS Layer Manager dialogue box
When
designing the dialogue, the educational aspect was considered very important.
Therefore, the number of functions is quite limited. No courses to educate the
CAD users should be necessary. This approach seems to have fulfilled its
purpose - the new systems were accepted very rapidly and there were few
question about the use. In future versions, more elaborate management of the
structure will probably be introduced.
In addition
to the Layer Manager, automatic assignment of layers has been embedded in all
functions of the AEC application program, and conversion programs from the
previous layering structure and back are available to the user.
Wednesday, November 20, 2013
Palace of Surakarta, By Budi Maryanto, ST
SURAKARTA palace built in 1708, it is characterized by sengkalan years in Stage Songgobuwana, namely NOGO MUOLUK TINITIHAN JAMNO, which shows the number in 1708, Nogo = 8, Muoluk = 0, Tinitihan = 7, jamno = 1, according sengkalan. Kraton Solo, is actually a transfer of KRATON Kartasura which runs on fuel by SUNAN YELLOW forces in the event of a war with china society. By Pakubuwana II, KRATON Kartasura moved to the village of SOLO.which later changed its name to SURAKARTA
SOLO palace photo
Monday, November 18, 2013
ISO LIST FOR MECHANICAL ENGINEERING DRAWING by BUDI Maryanto, ST
ISO 128-1, 2004 Technical drawings - General principles of
presentation - Part 1: Introduction and index
ISO 128-20, 1996 Technical drawings - General principles of
presentation - Part 20: Basic
conventions for lines
ISO 128-22, 1999 Technical drawings - General principles of
presentation - Part 22: Basic
conventions and applications for leader lines and reference lines
ISO 128-24, 1999 Technical drawings - General principles of
presentation - Part 24: Lines on
mechanical engineering drawings
ISO 128-30, 2001 Technical drawings - General principles of
presentation - Part 30: Basic
conventions for views
ISO 128-34, 2001 Technical drawings - General principles of
presentation - Part 34: Views on
mechanical engineering drawings
ISO 128-40, 2001 Technical drawings - General principles of
presentation - Part 40: Basic
conventions for cuts and sections
ISO 128-44, 2001 Technical drawings - General principles of
presentation - Part 44: Sections on
mechanical engineering drawings
ISO 128-50, 2001 Technical drawings - General principles of
presentation - Part 50: Basic
conventions for representing areas on cuts and sections
ISO 129-1, 2004 Technical drawings - Indication of dimensions
and tolerances - Part 1: General
principles
ISO 1101, 2004 Technical drawings - Geometrical tolerancing -
Tolerancing of form, orientation,
location and run-out - Generalities, definitions, symbols, indications on drawings
ISO 1302, 2002 Geometrical Product Specifications (GPS) -
Indication of surface texture in technical product documentation
ISO 6149-1 Connections for hydraulic fluid power and general
use - Ports and stud ends with ISO 261 metric threads and O-ring sealing - Part
1: Ports with truncated housing for O-ring seal
ISO 11926-1
Connections for general use and fluid power - Ports and stud ends with
ISO 725 threads and O-ring sealing - Part 1: Ports with O-ring seal in
truncated housing
ISO 13715, Technical drawings - Edges of undefined shape - Vocabulary and indications
ISO 2162-1, 1993 Technical product documentation; springs;
part 1: simplified representation
ISO 5459, 1981 Technical drawings; Geometrical tolerancing;
Datums and datum systemsfor geometrical tolerances
ISO 6410-1, 1993 Technical drawings; screw threads and
threaded parts; part 1: general Conventions
Thursday, November 14, 2013
THE SNAP by Budi M
Snap is one of AUTO CAD facility that serves to connect objects or lines precisely at the points of the desired line . When the AUTO CAD users want to connect a line to continue the line of AUTO CAD users will paste the line that will be made to the desired line . It will be difficult when the AUTO CAD users using the mouse . Because the object or the line should really stick sehinngga allow users AUTO CAD when it will make in the form of 3 -dimensional images , which in the process is preceded by the command region .
SNAP IN THE CIRCULAR FUNCTIONS
Snap function in the circular field is to determine the midpoint of a circular object field , specify quadran point of a circle and determine the tangent point well beyond the tangent line , and the tangent line , after determined its points then the AUTO CAD user is able to connect the line to the right.
Snap objects and their functions chart
Monday, November 11, 2013
MEMBUAT LAYER PADA AUTO CAD oleh BUDI MARYANTO,ST
Pada umumnya seorang pengguna AUTO CAD yang telah mahir menggunakan
AUTO CAD untuk menggambar sudah memiliki ketentuan-ketentuan yang sistematis
tentang manajemen layer. Manajemen layer pada umumnya menjadi tambahan
persyaratan teknis. Pada umumnya manajemen layer ini berupa dokumen atau
pedoman baku bagi seseorang pengguna AUTO CAD yang sudah mahir.
Setiap pengguna AUTO CAD yang telah mahir memiliki standar
masing-masing mengenai manajemen layer , akan tetapi pada prinsipnya sama yakni
mempercepat proses menggambar dengan AUTO CAD dan menyeragamkan hasil cetak
gambar. Meskipun pada proses menggambar dengan AUTO CAD layer dibuat terlebih
dahulu sebelum menggambar dengan AUTO CAD, tidak berarti gambar yang dibuat
dengan AUTO CAD tidak dapat diperbaiki. Akan tetapi hal ini tidak disarankan
karena akan banyak membuang waktu jika gambar yang kita gambar sangat komplek dan
tidak efisien dalam hal menggambar dengan AUTO CAD.
Manajemen layer pada AUTO CAD bertujuan untuk mengelola
komplektisitas gambar.
Layer dapat di bayangkan sebagai lembaran-lembaran transparan
yang menampung obyek gambar
Cara membuat layer pada AUTO CAD adalah sebagai berikut
11.
Ketik layer tekan enter pada command window,klik
format klik layer,atau klik ikon layer properties manager,
22.
Setelah muncul menu layer properties manager
klik kanan mouse pada layer 0,klik new layer,lakukan hal yang sama sesuai
dengan layer yang dibutuhkan pada gambar kerja
33.
Berikan nama pada layer sesuai dengan bidang gambar
yang akan di proses
44.
Pada control panel layer ubahlah properties dari
layer sesuai dengan kebutuhan akan gambar
Tuesday, November 5, 2013
MAKE AND TYPE LINE BY LINE OF MIND Maryanto , ST
In the mechanical engineering drawing lines is a very important part , the pull line results determine the working drawings that we will make , and can give meaning and a specific meaning in accordance with the terms of lines and line thickness , so be careful with the line if we are going to make a picture employment .
AUTO CAD as one of the software to provide a variety of drawing the line types are stored in a specific file . AUTO CAD users can avail this facility in accordance with the requirements of the image.
Make the type of line or load line with the term only done one time only for the same type of line . AUTO CAD users can create a kind of line by line type created by one or several types of lines at once or even any type of line we load it into the image file we're working on ,
How to perform load line form is :
1 . Click on the tool bar properties for the form that is in line or number two from the left on paper by layer
2 . Click on the other line that is under the
3 . After exiting display other menu , click load
4 . At the load menu , select the desired outline shape
5 . click on OK
1 . Click on the tool bar properties to form a line number three on the left of the posts by layer
2 . Select the desired line thickness
examples of applications of this type of line according to ( ISO 128-1982 ) on the working drawings
• Line Thickness ( 0.5 mm 0.7 mm ) is used to outline objects seen directly , line edge .
• The Thin Line ( 0.25 mm 0.35 mm ) is used for the bending radius of the shadow line , line size designation , projection lines , object pointer lines , line shading , lines short flashlight ,
• The Thin Line Free ( 0.25 mm 0.35 mm ) is used to limit the view of objects or parts of slices that are not exactly on the axis .
• The Thin Line with Zig - Zag ( 0.25 mm 0.35 mm ) display the lines are long sections of the workpiece )
• Disconnect Line Thickness ( o , 5 mm 0.7 mm ) is used to outline objects that other objects in front of him blocked , obstructed line edge .
• Disconnect Line Thin ( 0.25 mm 0.35 mm ) was used to outline objects obstructed , unobstructed line edge
• Point Thin Line Strip ( 0.25 mm 0.35 mm ) are used for flashlight line , the center line of a symmetrical object , a line indicating that the workpiece can be moved
• Point Line Strip , Thick on the tip and bend ( 0.5 / 0.7 0.25 mm / 0.35 mm ) is used for cutting the line object
• Point Strip Line Thickness ( 0.5 / 0.7 0.25 mm / 0.35 mm ) is used to line the surface will get additional work .
• Strip Outline Dual point ( 0.25 mm 0.35 mm ) is used to line the adjacent objects , moving parts , gravity lines , line objects in front of the cross- cut .
examples of this type of application tables and forms a line by line ( ISO 128-1982 ) on the working drawings
Monday, November 4, 2013
ORDERS LENGTHEN
Lengthen command in AUTO CAD serves to extend the stripe size of an object . With a command LENGTHEN AUTO CAD users can extend the size of the circle or arc , line size objects .
In order LENGTHEN an AUTO CAD users can extend the object by means of:
1 . Dragging an object with a dynamic endpoint
2 . Determine the length of a line or arc to be made as a percentage of the total length of the line or arc
3 . Determine the length of a line or arc of an endpoint
4 . Determine the scope of a line or arc length absolute total of the object object
In this LENGTHEN command , AUTO CAD users generally prefer using techniques Dragging endpoint . Dragging an endpoint using the technique , an AUTO CAD users no longer have to provide a measure of the extend line , but quite mendragging endpoint until the desired size of the AUTO CAD users themselves .
Way to run a command lengthen premises endpoint is dragging techniques ;
1 . On the Modify menu , click Lengthen , or in the command window type lengthen
2 . Type DY at the prompt Select an object or [ DELTA / Percent / Total / Dynamic ] : DY
3 . Select and click on the blue line with the left mouse , the line will be extended
Images , irregular octagon before the command was given to AUTO CAD LENGTHEN
4 . Drag endpoint to endpoint selection and specify the new
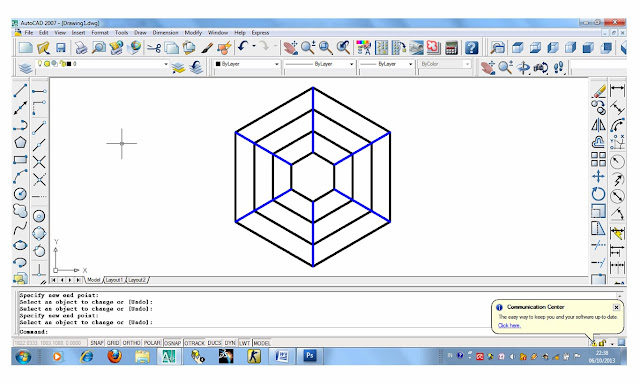
Images , irregular octagon after the command was given to AUTO CAD LENGTHEN
Command window text editor on AUTO CAD
Automatic save to C : \ Users \ MYNOTE ~ 1 \ AppData \ Local \ Temp \ Drawing1_1_1_6500.sv $ ...
Command : LENGTHEN
Select an object or [ DELTA / Percent / Total / Dynamic ] : DY
Select an object to change or [ Undo ] :
Specify new end point :
Select an object to change or [ Undo ] :
Specify new end point :
Select an object to change or [ Undo ] :
Specify new end point :
Select an object to change or [ Undo ] :
Specify new end point :
Select an object to change or [ Undo ] :
Specify new end point :
Select an object to change or [ Undo ] :
Specify new end point :
auto cad 2007
In the present era , the development of technology was very
fast . Almost all aspects of life began to be touched with
the name of technology . With all the technology feels more
easy to do . Various innovations do not stop
to increase the use and application of technology in
human life . One of the rapidly evolving technology
is CADD ( Computer Aided Design and Drafting ) . development
This technology aims to make it easier for designers
and drafter to visualize their ideas into form
image .
AutoCAD is a CAD program that is quite well known
by the designer and drafter because it offers a variety of
ease and excellence . AutoCAD shown to facilitate
the work of the designer and drafter in visualizing
ideas and their ideas . AutoCAD created or issued
by Autodesk Corporation in 1982 . Starting from the first
coined until the latest products launched ,
AutoCAD continues to experience growth and able to take
to the development of current CAD technology .
AutoCAD is an application program that is used to
drawing and design , such as for modeling ,
create architectural drawings , machinery , civil, electrical , manufacturing , and
others. With AutoCAD , the design process becomes easier ,
fast , and accurate . AutoCAD has excellent facilities
complete . A design can be created with AutoCAD
with easy to edit when there are mistakes and shortcomings ,
has a very varied picture layout , scale
can be changed , adjusted to the paper size , and so
practical storage.
1
B. Overview CADD
Computer Aided Design and Drafting or better known as
CADD , has been there since 1964 but their use is still
limited to the mainframe . In 1982 , the system began to be known
CADD on a PC with a software that has
AutoCAD name . Now we have to know AutoCAD software
to release 2007 with great capabilities and benefits
and awesome that no longer forms a 2D image
or 3D that can not be drawn by the program .
In AutoCAD there is also a programming language called
AutoLISP that allows us to develop their own
AutoCAD software and can be used as a program
specific , tailored to our needs and requirements .
CADD operator communicates with the computer through input
devices , such as keyboard , mouse , digitizer . In addition , other input
can come from a scanner or file with another extension
such as 3DS , DXF , DXB .
CADD software that will be discussed are AutoCAD , where
The software has great flexibility . AutoCAD
not only be used for specific applications , such as architecture ,
mechanical , geodesy , or machines , but has the ability
to draw anything . If we want to make AutoCAD
a dedicated software , we can add that
called " 3rd party software " , for example :
• Autodesk Architectural Desktop for architectural applications .
• AutoYatch to design boats and sailing boat ( yacht ) .
• Auto - Site - Lite lighting calculations for applications .
• Autodesk Land Desktop for civilian applications , mapping , and
urban design .
• AutoCAD -MAP for GIS applications .
• SEW - CAD for fashion and textile applications .
• Autodesk Mechanical Desktop for mechanical applications .
With the software mentioned above , we can more
increase productivity in areas of our work .
Subscribe to:
Posts (Atom)